OVERVIEW
The adoption of the “Initial International Maritime Organization (IMO) Strategy on Reduction of Greenhouse Gas (GHG) Emissions from Ships” by IMO Resolution MEPC.304(72) in April 2018 demonstrates IMO's commitment to support the Paris Agreement. The IMO strategy includes initial targets to reduce (as compared to 2008 levels) the average carbon dioxide (CO2) emissions per “transport work” by at least 40 percent by 2030, aiming to pursue 70 percent reduction by 2050; and an ambition to reduce the total annual GHG emissions from shipping by at least 50 percent by 2050. Technical approaches, operational approaches and alternative fuels may be used to achieve these goals.
The near-term regulatory changes and the future impact of the IMO's GHG targets for 2030 and 2050 should be considered when making the long-term decision on fuel selection. Liquefied natural gas (LNG) is a relatively mature low-carbon fuel, comprised primarily of methane. Its carbon to hydrogen (C/H) ratio offers a reduction in CO2 emissions of up to 20 percent compared to baseline heavy fuel oil (HFO). In combination with latest technological improvements and/or operational measures, LNG may be a viable option to meet the 2030 emission reduction goals.
This paper focuses on selected practical considerations for LNG as a marine fuel and summarizes the relevant vessel design and operational aspects with reference also made to relevant technological advancements.
The information provided can support the decision-making process for future ship designs, propulsion systems, and fueling strategies. It is an overview of the key aspects considered for LNG as fuel, addressing bunkering, vessel arrangements, fuel containment, fuel gas supply systems, single gas and dual-fuel (DF) main engines. The adaptation of LNG as fuel depends on case-specific requirements and therefore the information provided in this paper concentrates on the areas that apply broadly to LNG as fuel installations.
This document provides practical pointers in the use of LNG as marine fuel and is intended to supplement the ABS Advisory on Gas and Other Low Flashpoint Fuels. Information provided in this document is generic in nature. For specific guidance on LNG as marine fuel the local ABS office may be contacted.
LNG AS FUEL FOR THE REDUCTION OF GREENHOUSE GAS
LNG as a fuel is one of the options that an owner might use in combination with technological and operational improvements to meet IMO 2030 CO2 reduction targets.
In a comprehensive approach, the first step would be to benchmark where an owner's fleet is currently in its emissions reduction plans. Then look at the intended operating profile of the vessel/s and determine how an LNG fueled vessel would fit into the company's plans and what savings they could expect.
The operating profile impact is not to be underestimated, as depending on the fuel system selected a vessel may not get the expected 20 percent reduction. Burning of natural gas in boilers to control tank pressure has been used as a convenient means of controlling LNG tank pressures and temperatures and maintain them within acceptable limits. However, this excess consumption simply to control and maintain pressures affects the overall carbon footprint.
Type of containment system used, boil-off gas (BOG) management system in place and combustion process adopted have an impact on total GHG emissions.
INITIAL LNG CONSIDERATIONS
IMPACT OF OPERATIONAL PROFILES AND ROUTES ON VESSEL DESIGN
Most vessels are designed based on a defined operating profile. Hull form has also typically been a significant influencer on vessel design. For liquefied natural gas (LNG) fueled ships, the design of the LNG fuel containment system needs to consider both the optimal operating profile while the vessel is in transit and the undesirable conditions such as when the vessel stops, loads, awaits orders, etc.
For example, a sample aframax tanker in the European sector spends 30 percent of its time idle with no main propulsion power with an average speed of only 10 knots compared to a design speed of 14.5 knots. Very large ore carriers/bulk carriers often spend about three weeks in port waiting to load and about another three weeks in a destination port waiting to discharge. Along with operating profiles, designs are to consider the dynamic characteristics of LNG fuel properties and that the associated fuel containment system can cope with these extended periods with low rates of gas consumption.
This change in thinking may mean that the first fuel system proposed may not be the one that is best suited to everyday operations. The design is to be flexible enough and well suited to meet normal trading patterns.
In-depth voyage and vessel operations profile analysis is required to establish likely parameters and guide system design and equipment specifications (for example, matching tank maximum allowable relief valve setting of a cargo tank [MARVS] to meet likely fuel supply saturated pressure).
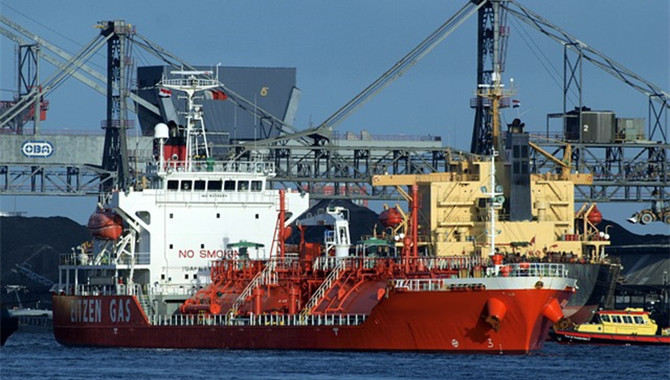
OWNERSHIP COST CONSIDERATIONS DURING CONCEPTUALIZATION
Actual operating profile and fuel to be used for each part of the journey needs to be considered during cost analysis.
There are multiple different configurations that could be utilized between propulsion power and electrical power supply by auxiliary generators such as single gas fuel generators coupled with dual-fuel (DF) or conventional liquid fuel generators. In certain cases, it might be better to fit LNG fuel to the main engine and have the auxiliary generators on liquid fuel.
Reliquification plants are an option, but a life-cycle cost analysis might be necessary to justify the capital expenditure (capex), operational expenditure (opex) and environmental costs.
For redundancy, having a means of replacing a pump or valve in service may be cheaper than having two pumps or valves. However, redundancy replacements might not be as straightforward in many cases. Careful attention needs to be paid towards the redundancy requirements. With regards to the International Code of Safety for Ships Using Gases or other Low-Flashpoint Fuels (IGF Code), essential services are to be provided by DF gas consumers since single point failure of a gas component will revert to diesel operation. For single gas fuel consumers redundancy is required for essential services.
CHARATERISTICS OF LNG
LNG is a mixture of several gases, in liquid form, principally composed of methane (CH4), with a concentration that can vary from 70 to 99 percent by mass, depending on the origin of the natural gas. Other hydrocarbon constituents commonly found in LNG are ethane (C2H5), propane (C3H8), and butane (C4H10). Small amounts
of other gases, such as nitrogen (N2), may also be present. Natural gas reserves are significant; with the International Energy Agency (IEA) estimating reserves at current usage rates (January 2011) are over 250 years.
When liquefied at approximately -162° C, the volume required for natural gas is reduced to about 1/600th of that required when in the gaseous state. In this condition, LNG is stored in tanks where the heat ingress leads to the generation of boil-off gas (BOG). The BOG is consumed by the engines or is re-liquified in order to maintain the LNG tank pressure within acceptable limits. The LNG saturation vapor curve and its effect on bunkering is to be fully comprehended to improve bunkering.
Both marine slow-speed two-stroke engine manufacturers, MAN Energy Solutions and Winterthur Gas & Diesel (WinGD), offer DF internal combustion engines. However, each manufacturer has selected a completely different combustion process for when the engine operates in gas mode. The two different gas mode combustion concepts are low-pressure (LP) gas engines using the Otto cycle and high-pressure (HP) gas engines using the Diesel cycle.
The WinGD LP DF engines (X-DF) utilize the Otto process in gas mode and the conventional Diesel process when in oil mode. The MAN HP DF engines (ME-GI) use the Diesel combustion process in both oil and gas modes. For both concepts, the gas is ignited by a pilot injection of liquid fuel from the conventional fuel injection system, or a dedicated pilot fuel system. The point during the combustion cycle where the gas is injected dictates the required gas supply pressure.
The WinGD X-DF is designed to operate at a gas supply pressure of up to 13 bar, and the high-pressure MAN ME-GI uses gas delivered by a direct injection system at approximately 300 bar. The two different designs lead to different combustion concepts, Otto cycle for the X-DF and Diesel cycle for the ME-GI, and therefore have different performance and emissions characteristics. A recent announcement by MAN involved the development of their low-pressure DF engine, ME-GA.
Table 2 highlights some of the key similarities and differences between the slow speed DF concepts. The similarities are limited to, the pilot fuel oil quantities required to start the gas combustion process, the minimum engine load that the engine can achieve when operating in gas mode, and the fact that both concepts are sulfur oxides (SOx) compliant when using sulfur compliant fuel for the pilot fuel.
Overall, the suitability of a specific concept, or engine type, to a ship is very much a case-specific decision. For some, it may simply be that they are not comfortable with HP gas or the increased complexity and cost associated with HP fuel gas supply systems. For others, it may be the concerns with Otto cycle being sensitive to a number of operating parameters (Methane Number, Ambient Conditions), or the GHG impact of methane slip.
Table 1: Otto vs Diesel Slow Speed 2-Stroke DF Engine Comparison
REGULATORY COMPLIANCE
Regulatory and classification requirements are in place for the use of natural gas fuel in marine applications.
The specific gas fueled ship (GFS) arrangements depend on the fuel containment, the fuel gas supply system (FGSS), and selected prime mover technologies. The link between fuel storage, fuel preparation and gas consumer is much more interdependent as compared to conventional fuels. Critical equipment and system design decisions cannot be made in isolation. The following sections are to be considered for the use of liquefied natural gas (LNG) as a marine fuel.
IMO REGULATIONS
The adoption of the Initial International Maritime Organization Strategy on Reduction of Greenhouse Gas Emissions from Ships by the Resolution MEPC.304(72) in April 2018 demonstrates the IMO's commitment to support the Paris Agreement. It includes a vision to phase out GHG emissions from international shipping within the century and may be an active driver for member States to initiate decarbonization and reduction of GHGs using policies and procedures.
The IMO's International Code of Safety for Ships Using Gases or other Low-Flashpoint Fuels (IGF Code) applies to ships to which the SOLAS Part G Chapter II-1 applies and contains only detailed prescriptive requirements for LNG under Part A-1 of the Code. Other low-flashpoint fuels may also be used as marine fuels on ships falling under the scope of the IGF Code, provided they meet the intent of the goals and functional requirements of the IGF Code and provide an equivalent level of safety. This equivalency is to be demonstrated by applying the Alternative Design risk assessment process and SOLAS novel concepts approval procedure of SOLAS regulationII-1/55, and as required by
2.3 of the IGF Code.
RISK ASSESSMENT
The following basic operations and routing items are to be considered:
•Type of vessel and associated cargo operations (e.g., offshore support vessel (OSV), tug, container carrier, bulk carrier)
•Expected trade route (including roundtrip or one way).
•Where to bunker the vessel, how often to bunker, bunker providers, bunkering time duration.
•Vessel bunker tank sizes have increased considerably. Larger tank sizes require careful planning for cargo transfer operations as the operation might take weeks in port.
•Vessel build location and maintenance/ repair locations which might influence scheduled and unscheduled delays. Choice of fuel between these locations and plan to manage operating expenditure (opex) costs.
These basic considerations can impact on choices and selections for a vessel and in determining engine choice, gas fuel handling system and amount of redundancy needed.
Contingency planning is necessary to account for unexpected vessel repairs (emergency drydocking, hull inspection, engine repair, major damage) to accommodate tank emptying, gas freeing and subsequent return to service.
Extensive prior planning for integration of LNG fuel, methods and procedures with crews, fuel suppliers, transporters, port authorities and regulators is necessary.
Source: ABS
The opinions expressed herein are the author's and not necessarily those of The Xinde Marine News.
Please Contact Us at:
media@xindemarine.com
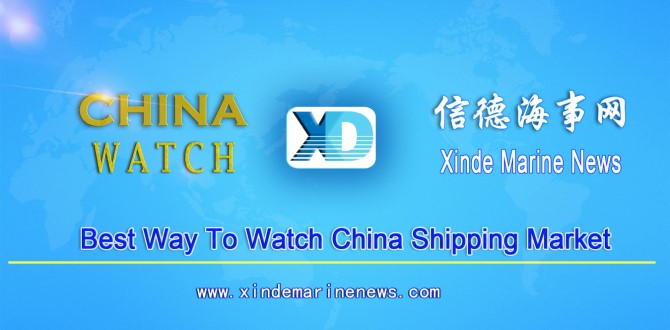