By upgrading, converting, or modernising onboard systems, MacGregor service projects help to boost the performance and extend the lifespan of existing ships.
With a core commitment to maintaining the operational safety and performance of its market-leading cargo- and load-handling solutions, MacGregor closely supports its customers from the design phase to the end of the vessel lifecycle.
However, when ships are confronted with the real-world challenges of maritime operations, regular maintenance is not always enough to keep them functioning optimally or in compliance with regulations, while certain systems may become obsolete during the vessel’s normal lifespan. In such cases, MacGregor can offer a comprehensive range of service projects covering upgrade, conversion, modernisation, replacement, retrofit, refurbishment, and steel repair.
Enhancing safety, sustainability, and cost-efficiency
Applicable to merchant and offshore vessels and systems including deck machinery, cranes, ro-ro equipment, and hatch covers, MacGregor service projects aim to maximise the performance and lifespan of existing vessels. Projects range from minor modifications to major overhauls and include a turn-key service encompassing design, delivery, installation, and commissioning. Depending on requirements, they can be delivered as a standard package or a tailored solution.
“Ship owners today are always looking for ways to improve safety and sustainability in line with regulations while cutting costs,” says Eduardo Prat, Head of Service Projects. “By upgrading a system or replacing it with the latest version, we help to make ships safer and more fuel efficient, with benefits for the environment as well as the owner’s bottom line.”
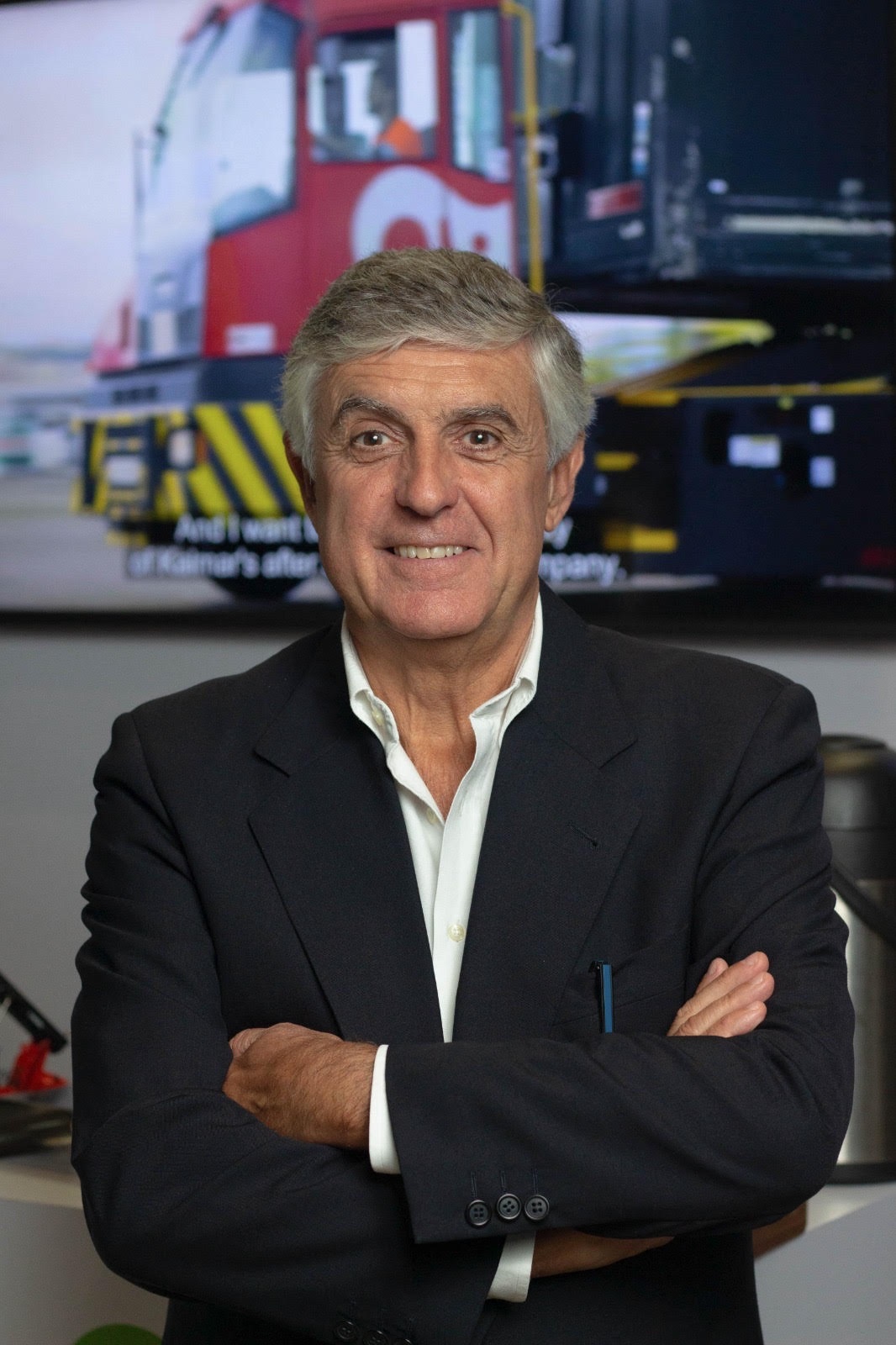
Eduardo Prat
As an example of how service projects can enhance safety, Prat refers to the electrical interconnection of anchor windlasses – a project MacGregor is currently discussing with a major shipping company. “In a traditional set-up with the windlasses operated separately on opposite sides of the ship, if the windlass carrying the anchor fails after the anchor is dropped, the safety impact can be significant,” he explains. “With the windlasses electrically interconnected at the bow, one acts as a back-up for the other, reducing the risk of an incident.”
Other safety-oriented services provided by MacGregor include a mooring drum upgrade in which deteriorating brake rims are renewed with stainless steel to improve their performance and extend their service life. Prat also points to the upgrade of deck cranes into personnel-handling systems, which allows seafarers to be transferred safely from an auxiliary vessel to a tanker, for instance, with safety measures implemented based on class specifications.
In some cases, MacGregor’s services directly address a specific regulation. For example, its Brake Test Kit service is a response to updated requirements for testing the load capacity of drum-band brakes following modification or repair. It applies to mooring systems from MacGregor brands – such as Hatlapa, TTS Kocks, and Pusnes – and requires only a minor modification.
Another relatively simple upgrade is the installation of MacGregor Soft Flaps on board ro-ro and ro-pax vessels. Applied to the end of the ro-ro ramp, Soft Flaps significantly reduce noise from embarking and disembarking vehicles, benefiting crew, passengers, port staff, and residents of port-adjacent communities. They are also easier to maintain and replace – and better able to withstand the impact of heavy vehicles – than steel flaps, thus reducing total cost of ownership.
One of MacGregor’s most effective services, Prat continues, is its variable frequency drive (VFD) upgrade for Porsgrunn steering gears. “In many cases, a vessel’s steering gear is constantly in operation – and therefore constantly consuming energy – but with MacGregor’s VFD upgrade, it only works when needed to turn the rudder,” he says. “In this way, the service enhances energy efficiency to cut both carbon dioxide emissions and operating costs.”
According to Matty Harders, Manager Deck Machinery, Steering Gear & Compressors, Global Services, MacGregor’s VFD upgrade exemplifies the company’s more “proactive” services. “We generally carry out service projects in response to a request from a customer to resolve a specific, often critical, challenge they are facing,” he says. “The VFD upgrade isn’t necessarily something a customer needs; rather, it’s a practical and proactive measure they can take to reduce their environmental impact while saving money – a classic ‘win-win’ situation.”
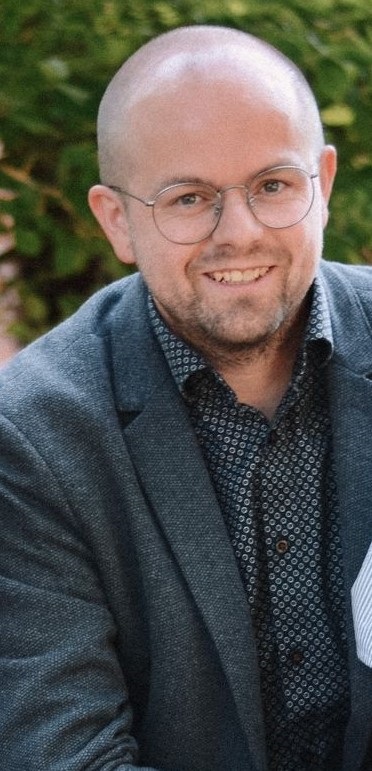
Matty Harders
Harders adds that the service can cut annual vessel CO2 emissions by 50 tonnes and yield a return on investment within 14–20 months.
A skilled and experienced global workforce
Since MacGregor exclusively offers service projects for its own equipment and that of its brands, customers can rely on engineers’ in-depth knowledge of the system being serviced. With almost 50 international brands operating under the MacGregor umbrella, its equipment is on board around 40,000 vessels worldwide, meaning approximately every second ship at sea may benefit from a MacGregor service project.
Geir Roland, Director of Service Projects, says the company’s multi-brand, multi-divisional structure ensures its combined workforce possesses a comprehensive and diverse skillset.
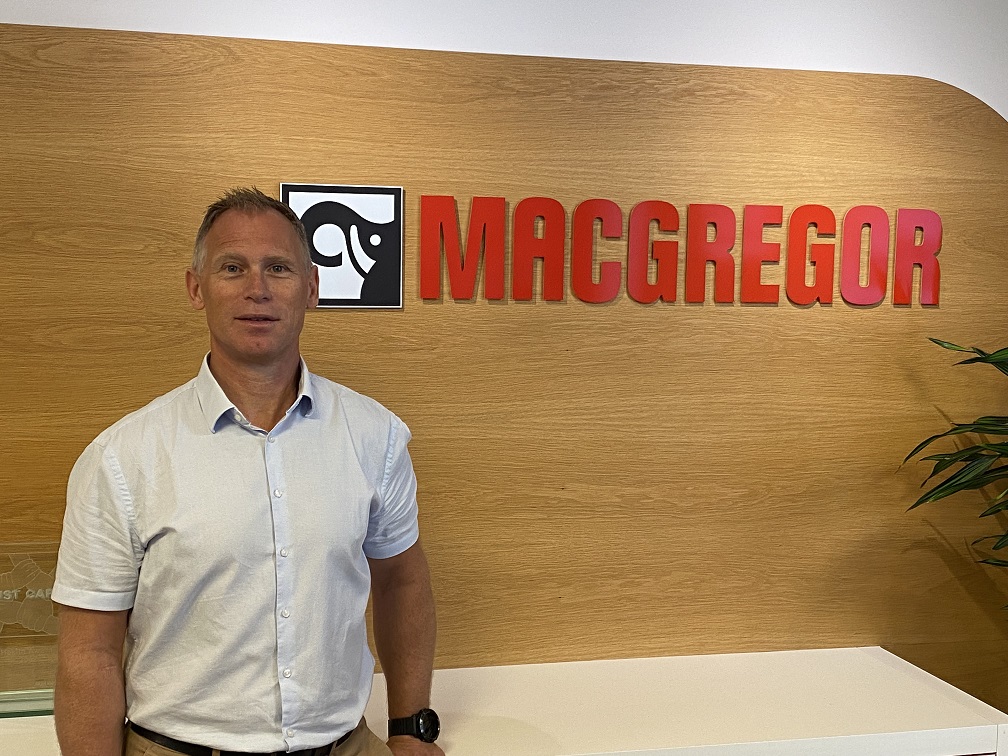
Geir Roland
He also emphasises that with personnel from so many makers and departments, the service project team is strong, has significant expertise, and offers a variety of perspectives to help MacGregor customers with their challenges. This allows the company to plan and execute a broad range of complex projects with consistent enthusiasm, proficiency, and know-how.
Roland adds that MacGregor employees are highly experienced, serving the company for an average of 17–18 years. In addition, thanks to MacGregor’s global service network, which comprises approximately 900 service specialists at around 40 service centres in 31 major ship-owning countries, projects can be executed wherever a customer requires support.
“Through our service projects, we provide any service the ship owner needs, however big or small, to operate their vessels as safely, sustainably, and cost-efficiently as possible – for as long as possible,” says Roland. “Ultimately, the goal is to extract maximum value from existing vessels by boosting their performance, facilitating their ongoing regulatory compliance, and extending their lifespan.”
source:MacGregor
source:MacGregor
The opinions expressed herein are the author's and not necessarily those of The Xinde Marine News.
Please Contact Us at: