As ship owners around the world respond to environmental regulations that are
changing the way vessels are powered, there is less certainty than ever around what future vessels will look like. The markets of the future are equally uncertain; current widespread supply chain disruption and economic turbulence will impact trade flows, vessel utilization and profitability across shipping segments, as well as affecting fleet expansion and renewal plans.
These trends create a challenging environment for planning future ship operations, which is particularly problematic in
an industry renowned for longevity. Maintenance is a
critical consideration for optimizing the availability and useful lifecycle of ships, and a significant factor within total lifecycle cost and operational expenditure. But with little insight into fleet composition or usage in the future, long-range planning is definitely not a simple task.
That’s why Accelleron commissioned a survey for ship owners and operators, aiming to shed light on how maritime companies approach maintenance and servicing of their turbochargers in particular, and how this can continue to develop to meet the needs of ship owners and operators in future.
The survey highlighted five key areas that ship owners and operators feel strongly about, which we’ll be looking into further in the future here on charge!. In the meantime, read on for a more general overview.
The need for change
According to the responses to the survey, there’s a need for improvements in the way turbochargers are serviced and maintained. This is evident in the frequency of unplanned downtime, with 42% of companies surveyed reporting disruption in the previous year due to turbocharger-related issues. Improving the reliability of turbocharger technology is a top development priority for 91% of respondents, succeeded only by the need for efficiency improvements. The drive for greater reliability is a goal we share here at Accelleron, with
servicing and maintenance helping our customers to avoid unplanned downtime.
Controlling service cost
The rising costs associated with turbocharger service and maintenance is also a concern for several companies, with 38% noting an upward trend. In part, this is led by the growing demand for turbocharger servicing, suggesting that in some cases the machinery selected by operators requires more frequent service support. Global prices of labor and materials are also a factor, driving up the cost of spare parts and service engineers. In the short term, during the COVID-19 pandemic, restrictions on movement and new health and safety procedures also contributed to growing costs, although some of these costs can be mitigated by using
Accelleron's range of service agreements.
Long-term service agreements
Around 60% of companies reported that turbocharger service costs are remaining stable. This perhaps correlates with the 61% who are engaged in long-term service relationships with their turbocharger supplier, engine supplier or specialist service company. Among other advantages, contractual service arrangements,
such as Accelleron's Turbo SmartCare, offer greater scope for flattening costs across a long period, with the ability to absorb and adapt to short-term price increases. For those entering long-term service agreements, minimizing cost and improving cost predictability are key considerations, coming close behind technical competency and availability of spares and engineers.
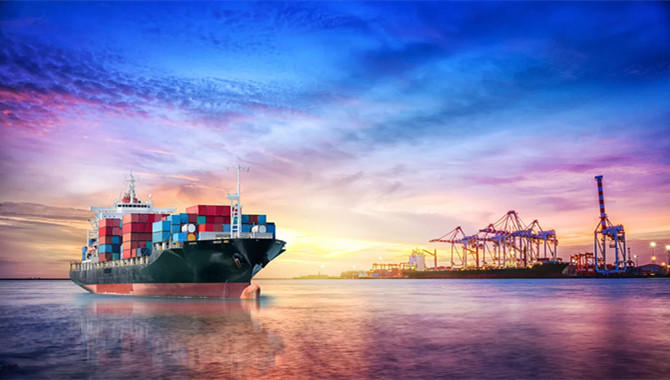
Image credits: Aun Photographer/Shutterstock
Digital monitoring
There are many avenues for reducing the cost of turbocharger servicing. For 63% of respondents, condition-based monitoring and predictive maintenance hold the most potential. However, there is a lag between companies recognising this and implementing the digital technologies that will enable it; just 51% of companies are currently using digital monitoring of turbochargers. A further 21% are planning to introduce digital monitoring, while the remainder prefer manual monitoring. Features such as
Accelleron's Turbo Insights are key, using digital solutions such as
compressor maps to help customers to get ahead.
Future service advances
The widespread belief in a digital solution to optimizing maintenance was reinforced when respondents were asked about future technologies with the potential to support machinery servicing. The use of artificial intelligence or machine learning was the most enticing prospect for 39% of companies, with 92% placing it in their top three. Other technologies with the potential to improve future service and maintenance include advanced materials to reduce costs and improve durability, cited by 36% as the top priority to be explored by technology and service providers. Accelleron is also a firm believer in upgrades,
helping customers to save money and reach sustainability targets.
These are just some of the headline details from the survey, highlighting the issues that are most important to ship owners and operators. We’ll be bringing you some of the finer details, and highlighting the ways Accelleron can help, soon.
Source: Accelleron
The opinions expressed herein are the author's and not necessarily those of The Xinde Marine News.
Please Contact Us at:
media@xindemarine.com
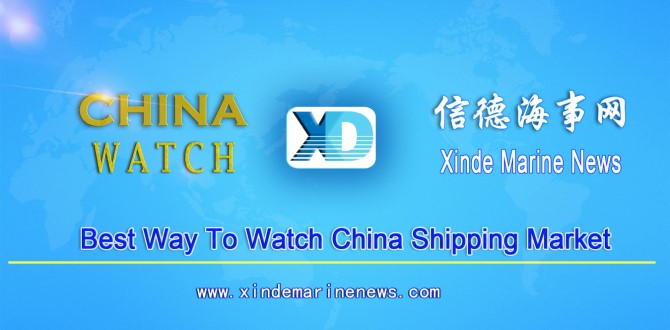