Numerous innovations are being presented this week at the world's leading trade fair WindEnergy Hamburg. Until Friday, the entire portfolio of the wind energy industry on land and at sea can be seen at Hamburg Messe und Congress with more than 1400 exhibitors from 37 countries.
Ideas for 20MW+ floating wind
The German wind energy consultancy AEROVIDE presents a 20MW+ floating offshore concept with an unusually shaped three-legged semi-submersible floating platform, a fully-integrated medium-speed drivetrain, a three-bladed downwind rotor with a controlled free yaw system, and a rotor diameter of roughly 280 metres. Managing director Markus Rees explains: “This large-scale floating concept, still an early-stage product development, is based on an internal evaluation of ideas as well as 40 years of in-house wind turbine design know-how and experience. Since the very first exhibition, AEROVIDE has always regarded WindEnergy Hamburg as the most important event in Europe to showcase new ideas and projects to international wind professionals.”
Direct-drive turbine pioneer Enercon presents a new 6.0MW E-175 EP5 turbine for low wind conditions with a 175m rotor, currently one of two largest onshore rotors outside the Chinese supply market. The introduction follows only weeks after the German exhibitor Nordex announced their 6.22MW high-speed geared model N175/6.X which likewise features a 175-metre rotor diameter. Both prototypes are planned for 2024, propelling European onshore turbines well into a new 170m+ rotor size class. This offers both challenges and opportunities for other specialised WindEnergy Hamburg exhibitors to advance and benefit.
Winergy, a Flender brand, present themselves explicitly in their new role as suppliers of wind turbine drivetrain systems at WindEnergy Hamburg. In the past the company was mainly known for gearboxes. Their focus is on the medium-speed HybridDrive drivetrain concept that combines the gearbox and generator in a single product assembly for large-scale onshore and offshore applications. The exhibitor displays a full-scale 5-6MW hybrid drive system including a low-speed coupling developed in-house. Furthermore, Winergy highlight a novel compact, oil-cooled generator option called PMG.
A 30MW test rig
ZF Wind Power, a supplier of drivetrain systems, has expanded its portfolio in a similar manner, presenting a new Test & Prototype Centre as well as a new, advanced service approach called ‘Thrive.’ The latter is described as ‘linking products, processes, and digital concepts for continuous availability and maximum output.’ What ZF have announced as ‘the world’s most powerful’ 30MW validation test rig is an innovative system supporting the development, testing and validation of complete next-generation, fully-integrated powertrains for onshore and offshore wind turbines. WindEnergy Hamburg visitors can see an impressive visual representation of this large-scale test centre, equipped with a 30MW electric drive motor and designed for torque loads of up to 45MNm and bending moments as high as 64MNm. The system can thus be used for realistic simulations of rotor-induced loads. Six metres in length, the rig will be used to test the dynamic behaviour of main bearings, gearboxes and generators at the full-system level. It will be installed at ZF’s production facilities in Lommel, Belgium, and become operational in 2024.
The bearing specialist Eolotec showcases ReSRoB – short for Repair-Solution Rotor Bearing –, an innovative solution for up-tower replacement of the main shaft spherical roller-bearing. These bearings are an integral part of popular high-speed drivetrains with three-point gearbox support.
Eolotec teamed up with the bearing supplier and WindEnergy Hamburg exhibitor Schaeffler to develop the new split spherical main roller bearing concept for weather-independent up-tower replacement. The solution presented in Hamburg reduces costs by at least 20-40% compared to conventional methods requiring rotor and drivetrain disassembly and the deployment of an expensive crane, explains Eolotec CEO Wolfgang Losert. In the traditional approach the defect component is exchanged at the factory, followed by reassembly at the site, which involves significant costs and risks.
Tenth anniversary
Regarding the importance of WindEnergy Hamburg for his company, Losert comments: “It is definitely this year’s key event for us, and all our new products, including the first main bearing replacement solution, had their premiere here. And we could easily bring in even our largest exhibit, a complete 24-tonne main bearing unit, and put it on display. Hamburg is thus the perfect place to meet existing and potential new customers from all over the world without having to travel far. Seeing friends and partners again is what we have been looking forward to most after the COVID-19 disruption. Apart from that, we are also celebrating our tenth anniversary here at the fair.”
LiftWerx Europe have developed an innovative up-tower crane technology for a safe, environment-friendly, cost-effective exchange of wind turbine main components, including gearboxes, without requiring expensive conventional ground-based cranes. The company recently kicked-off its European operations after achieving significant growth in North America, says managing director Eelko May: “We had a great start with executing our first gearbox exchanges for Scottish Power in the UK. The execution went smoothly and with very positive feedback from our client. LiftWerx is excited to be at the highest-impact wind event worldwide – WindEnergy Hamburg. Many clients and business relations have been longing to meet face-to-face, and we are looking forward to making fresh plans with them as inputs to bringing new solutions to the market.”
The US oil and gas giant ExxonMobil showcases lubricants and services for the wind sector, including ‘fill-for-life’ lubrication solutions designed to last for the entire service life of the bearing without requiring an oil change. ExxonMobil also present their latest developments for predictive maintenance, including sensor-based solutions, the result of a collaboration with US-partner Poseidon Systems.
Turning challenges into opportunities
The Belgium-based exhibitor DEME Offshore has teamed up with the Dutch company Barge Master for the long-term development of a fully US Jones Act-compliant feeder solution for upcoming US offshore wind projects. Both exhibitors are developing motion compensation technology to be first deployed in a pioneering feeder concept for the US Vineyard Wind 1 project. Barge Master supplies four motion-compensated platforms to be installed on US-flagged barges to be towed by US-flagged tugs. The innovative solution is a key example on how challenges – in this case, the current lack of US-built installation vessels – can be turned into opportunities through the smart re-use of surplus barges from the oil & gas sector. The companies will explain to visitors how this integrated, high-tech solution will allow transporting even the largest components from US ports to DEME’s jack-up installation vessels. When a feeder arrives alongside an installation vessel, the Barge Master motion-compensation technology will ensure safe lifting operations, increasing efficiency. Several other WindEnergy Hamburg exhibitors who are involved in new feeder concepts for the US offshore growth market are showcasing their approaches and solutions, as well.
The opinions expressed herein are the author's and not necessarily those of The Xinde Marine News.
Please Contact Us at:
media@xindemarine.com
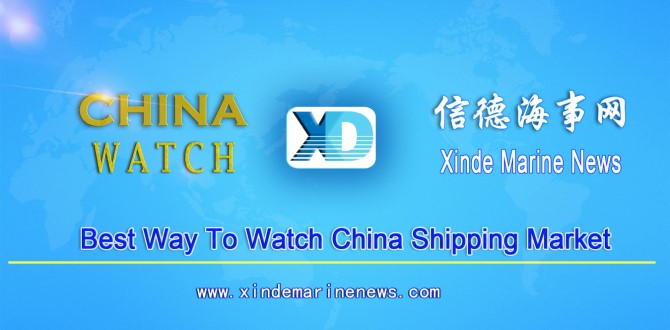