WinGD has reported successful factory acceptance tests for the first two X-DF2.0 dual-fuel engines to feature intelligent control by exhaust recycling (iCER). The new technology enables further improvements to fuel consumption and emissions performance from X-DF engines, building on a track record of reliable operations since they were introduced to the market seven years ago.
Effective combustion control is at the heart of the X-DF's performance and reliability. WinGD's low-pressure injection and pre-chamber design has been honed to minimise pilot fuel requirements, helping to achieve low NOx emissions while maintaining low overall fuel consumption. X-DF meets Tier III NOx emissions limits in gas mode without aftertreatment, a feature proven in more than 300 in-service engines recording almost 2 million operating hours and almost 500 X-DF engines on order.
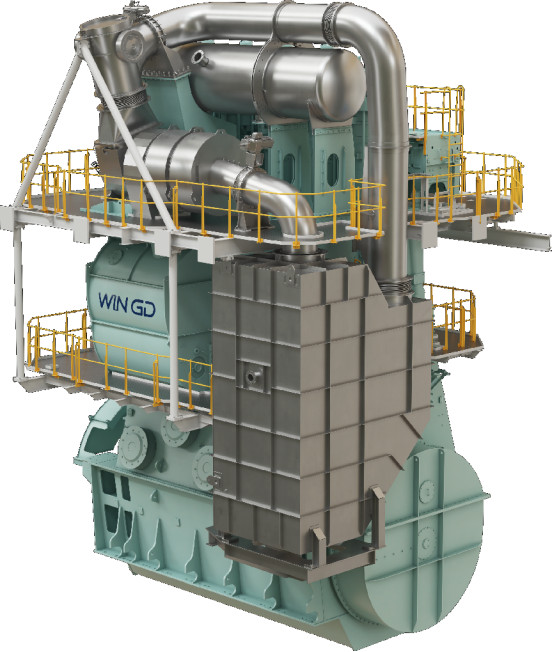
Targeting even more refined combustion control and optimised performance, in 2020 WinGD introduced the X-DF2.0 upgrade with iCER technology in 2020. This enables improved fuel consumption of around 8% in gas mode and 6% in diesel mode, as well as satisfying Tier III NOx emissions limits in both modes. It also reduces methane slip by up to 50%, giving it the lowest emissions of any similar combustion concept available. This performance improvement has been confirmed in recent factory acceptance tests for iCER with engine builders CMD in China and IHI Power Systems in Japan.
Dominik Schneiter, Vice President R&D, WinGD said: “We are delighted that the factory acceptance tests prove what we have known from our internal development validations; iCER optimises fuel efficiency and emissions without compromising the reliability and low capex that has made X-DF so popular over the past seven years.”
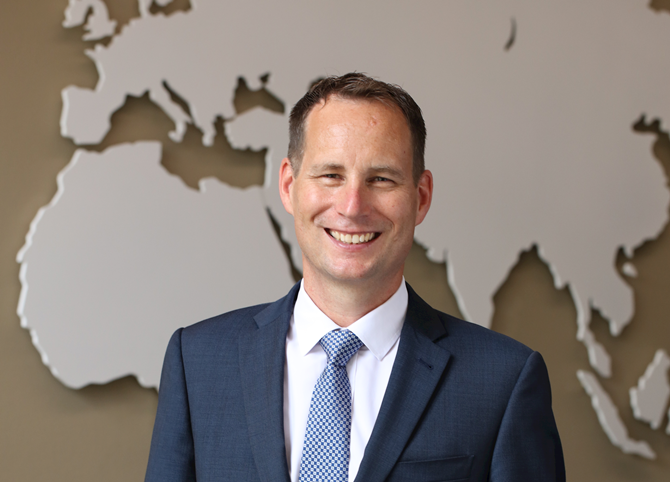
Using iCER's low-pressure exhaust recycling technology, engines can harness high recycling rates of up to 50%, allowing the engine to reach higher compression ratios that further reduce fuel consumption and emissions. Exhaust gas recycling can be used across the full engine load profile in both gas and diesel mode. In gas mode, the pilot fuel required is the same across the full engine load range.
The iCER technology has proven, clear advantages compared with high-pressure exhaust gas recycling technologies, which offer lower recycling rates, limiting the compression ratios they can reach. This lower combustion control capability of high-pressure EGR systems can typically leads to greater diesel pilot fuel injection at higher loads, impacting Tier III compliance, overall emissions and fuel efficiency.
X-DF2.0 offers operators the flexibility to optimise combustion with or without exhaust recycling. Using combustion stability mode without recycling, engines run on a ratio of gas and diesel fuel depending on engine load. X-DF’s well-proven injection technology minimises the amount of fuel used and enables engines to achieve stable combustion up to 100% load with the least possible amount of diesel fuel. For gas carriers, iCER can provide further flexibility through fuel sharing mode, which allows operators to use available boil-off LNG supplemented with diesel or VLSFO to reach desired ship speeds.
X-DF2.0 engines feature a number of patent-protected innovations based on the proven technology of the X-DF platform. They are available with either on-engine or off-engine iCER, helping engine builders and shipyards to optimise building and installation costs.
X-DF engines have been deployed across several merchant sectors, with particularly strong uptake on LNG carriers. The X72DF engine has become a popular choice for twin engine LNG carriers, with more than 200 installations and around 37,000 in-service running hours.
Source: WinGD
The opinions expressed herein are the author's and not necessarily those of The Xinde Marine News.
Please Contact Us at:
media@xindemarine.com
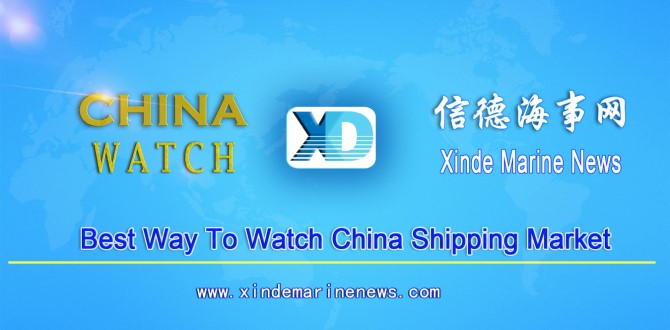